Thorlabs designs and manufactures a wide array of photonics equipment including motion control, imaging, light analysis, optoelectronics and optomechanics for the research, industrial, life science, medical, and defence segments. Founded in 1989 and headquartered in New Jersey, USA, the business employs over 1500 people worldwide that support a 15,000 strong product portfolio. Thorlabs customers range from academic researchers to major OEM accounts.
Thorlabs subjected Renishaw’s TONiC encoders to a battery of tests in direct competition with other optical encoder brands. The TONiC series outperformed the competition in every test and was selected to equip both the Thorlabs DDS600 600 mm long travel stage and the MLS203 microscope stage. Mark Robson, Engineering Manager at Thorlabs Ltd, UK, emphasises: “Renishaw’s TONiC series of encoders have enabled Thorlabs to deliver high-performance motion control products that our customers can depend upon. We evaluated TONiC, with respect to strict criteria, alongside other leading brands and found its performance to be best-in-class.”
The DDS600 low-profile stage demands high speed translation with high positional accuracy and is designed for surface mapping and characterization applications where there is a need to move a camera or probe at constant velocity while simultaneously capturing data. Thorlabs’ MLS203 X-Y scanning stages are drop-in replacements for the manual stages found on select microscopes, providing motorized X-Y positioning of microscopy samples. The MLS203 is compatible with inverted and upright microscopes from Nikon, Olympus and Zeiss. Optional adaptor brackets allow integration with other microscopes, optical tables and custom-built applications.
Higher performance
Measuring 800 mm (L) x 130 mm (W) x 50 mm (H), the DDS600 stage comprises a platform mounted onto a linear axis and driven by a linear DC synchronous motor. Linear motors eliminate the need for mechanical couplings, allow backlash-free operation of the motion stage and enable highly repetitive operations that would otherwise cause wear in a traditional motorized lead-screw. Thorlabs required a high quality velocity feedback solution to commutate the linear motor and meet the demanding metrology requirements of a high accuracy scientific motion stage. A compact high-performance encoder readhead was also specified in order to allow integration with low profile motion stages without sacrificing stage rigidity – as is common when removing material to accommodate larger package sizes.
Thorlabs carried out a failure mode analysis on the DDS600 design that highlighted the encoder signal cable as one of a few theoretical potential points of failure. Renishaw technical support shared data that provided information on cable lifetime expectations, which were subsequently evaluated independently by Thorlabs under soak test conditions to verify the failure mode assessment. These test results showed that Renishaw’s hi-flex encoder cables perform between 60% – 80% above the specified lifetime, giving Thorlabs the confidence to accurately predict product service life.
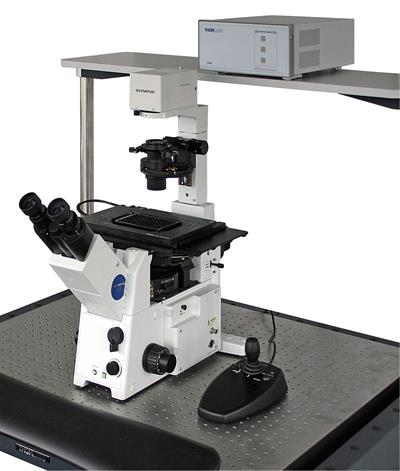
The DDS600 stage features a light aluminium construction to minimise the inertia of moving parts and high-rigidity recirculating bearings to increase load bearing capacity and lower maintenance costs. The scale of a typical encoder, attached in some way to the machine structure, is the basis for measurement performance of the system. In general, the scale and supporting substrate are made from different materials, which results in a thermal displacement mismatch due to differing values for the coefficient of thermal expansion (CTE). Although aluminium has a significant CTE compared with other engineering materials, such as granite, its extremely high thermal conductivity minimises the build-up of thermal gradients within the stage structure and allows effective real-time thermal error compensation.
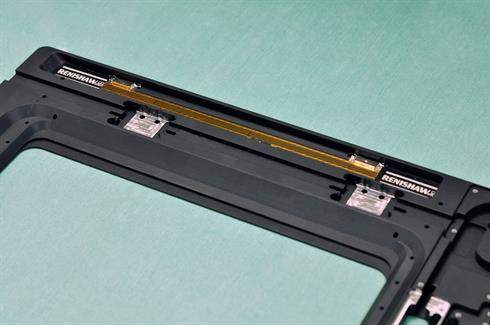
Thorlabs selected Renishaw’s TONiC readhead, which measures just 10 mm (H) x 35 mm (L) x 13.5 mm (W), with 5 nm resolution. It is combined with the RGSZ self-adhesive tape scale, which is essentially a gold-plated steel ribbon of 6 mm x 0.1 mm cross-section, as it significantly reduces thermal errors while satisfying other performance criteria. RGSZ is ‘mastered’ to the axis substrate with epoxy-fastened end clamps and expands precisely with it, ensuring the elimination of hysteresis for completely predictable metrology, as well as easy installation without the need for fixing holes. Differential movement between the scale and the substrate is effectively zero, even throughout significant temperature fluctuations.
Impressive DDS600 stage performance made possible by Renishaw’s TONiC encoder system includes: minimum 100 nm step-size, ±0.25 μm bi-directional repeatability and a maximum speed of 0.4 m/s.
During the design process for the MLS203 X-Y fast scanning stage, Thorlabs again used in-house testing to evaluate encoder performance. When choosing an appropriate position feedback system to be deployed within the MLS203, a potential concern was the risk of sample spillage and the effect this would have upon position control.
The dirt immunity performance of a number of competing encoder products was evaluated by the application of isopropyl alcohol (IPA), as a liquid contaminant, and common salt, in place of debris, to the encoder scales. Testing showed that Renishaw’s TONiC encoder system outperformed competing encoder products. This qualitative result allowed Thorlabs to determine that the TONiC encoder would not be susceptible to performance degradation as a result of foreseeable contamination.
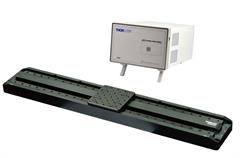
MLS203 X-Y fast scanning stages are equipped with a 20 nm version of the TONiC RGSZ encoder system on both X and Y axes of 110 mm and 75 mm, respectively. The MLS203 measures just 260 mm (L) x 230 mm (W) x 31 mm (H) and uses the same linear motor technology as the DDS600. In addition to criteria outlined for the linear stage, calibration is an essential operation that completes readhead set-up during final installation, with the optimum incremental and reference mark settings stored in the readhead’s non-volatile memory. Integral LEDs on TONiC’s readhead and interface allow optimum set-up and system diagnosis that further simplify installation during manufacture and servicing with particular benefit for multi-axis machines. Advanced MLS203 stage performance made possible by Renishaw’s TONiC encoder system includes: minimum 100 nm step-size, ±0.25 μm bi-directional repeatability, ±0.25 μm homing accuracy and a maximum speed of 0.25 m/s.
The premier encoder solution for compact stages
Key features of TONiC that enhance low profile / compact motion stage performance, in this case, include:
-
Cyclic error of typically ±30 nm offers ‘fine pitch’ encoder performance, allowing improved stage scanning performance with smoother velocity control and increased positional stability.
-
Compact encoder dimensions, 10 mm x 35 mm x 13.5 mm (H x L x W), permit integration with low-profile stages without loss of stage rigidity.
-
Excellent signal stability, supported by advanced filtering optics, in conditions unsuitable for most open optical encoders help minimise maintenance costs.
-
Outstanding encoder performance, with a maximum speed of 10 m/s, and low readhead mass of 10 g enables the development of faster low-inertia motion stages.
-
Long-life, robust, high-flex UL approved readhead cable in lengths up to 10 m, for connection between the readhead and interface, allows tight bend radii and optimisation of the cable track configuration.
-
Robust substrate-mastered scale minimises errors associated with changes to the local thermal environment – contributing to the accuracy and reliability of experimental results.