The future is one of driverless cars which will drastically change traffic and the experience of driving. This is one finding of a recent study by McKinsey & Company entitled “Autonomous Driving – 10 ways in which autonomous vehicles could reshape our lives.” McKinsey predicts various changes for manufacturers, including reduced development times, new competitors from high-tech and IT industries and the development of completely new business areas. Autonomous driving places very high demands on sensors, electronics and especially on the electromechanical components of current and future steering systems without which driverless cars would not be possible. Steering pinions are one of the standard components of these steering systems and are parts which must not only be manufactured in large volumes but also in top quality and at the lowest possible cost.
The specialists at KOEPFER, a subsidiary of the EMAG Group, are very familiar with electromechanical as well as traditional hydraulic steering systems. Jörg Lohmann, Sales Manager at KOEPFER, is in a perfect position to report the following: “Our customers’ goal is reduce the amount of production outsourced due to various processes and to ultimately reduce overall cycle times. One solution is to offer complete production lines at one site for strategic components. This also affords one the chance to review current setups and, in some cases, completely remove steps no longer necessary from the manufacturing process, aiming, of course, to sink production costs.” EMAG KOEPFER offers such modular vertical solutions alongside its highly efficient horizontal hobbing machines known for maintaining quality despite high productivity. The solution provided depends, of course, on the manufacturing strategy of the customer.
Large-scale steering pinion production
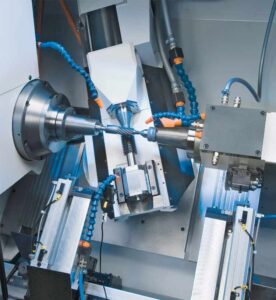
The K 160 features a high-speed portal loader with double rotary gripper to reduce the loading time to a few seconds. This challenge should not be underestimated when machining steering pinions, since the milling process often has to be carried out at a defined angle to existing slots, drilling templates or contours. A specially developed orientation device is the solution in this case. Lohmann continues: “Since the actual machining of the steering pinion only takes a few seconds, the idle times resulting from the loading and orientation processes can be reduced to an absolute minimum to maximize the machine’s efficiency. The high-speed loading solution we have developed enables production machining times of under 20 seconds to be achieved, which represents an enormous increase in productivity for an output volume of 100,000 to several million units.”
Complete production at a glance
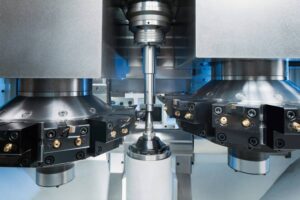
EMAG also developed a steering pinion manufacturing system based the company’s modular machine portfolio. EMAG uses the VTC 100-4 vertical pick-up turning machine, the customized version of the well-known VT 2-4 for turning the raw parts. The gear hobbing technology on the VLC 200 H vertical gear hobber then produces the toothing. The VLC 100 IH vertical hardening machine is then used for the inductive hardening process and the VTC 100 GT vertical turning and grinding center delivers the perfect finish and perfect surfaces in the final stage of the process. Should any additional finishing be necessary to the tooth profile due to quench distortion, the VLC 200 H, with skiving capabilities, is suited for the task.
Linking made easy – modular machines from EMAG
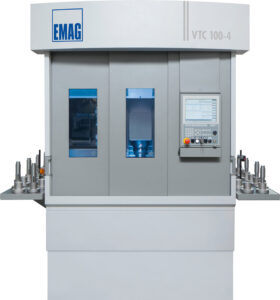
There are good reasons in favor of using EMAG’s modular machines in production lines, as the standard basic design delivers many major benefits. Each machine has a base made of Mineralit® polymer concrete, which has excellent damping properties to reduce vibration and improve component quality. EMAG’s typical design includes an automation system and parts storage facility configured to suit specific requirements, both of which are just as integral to the modular machine concept as the pick-up automation system, in other words the automatic loading and unloading from this parts storage facility. The entire process takes place in just a few seconds to maximize the machines’ output. As the storage component is at exactly the same height on all the modular machines, transporting the workpieces between them is greatly simplified. Comparatively simple automation components, such as conveyor belts, pick-and-place units and changers make it possible to link the modular machines as required. These simple solutions not only guarantee low costs, but also require very little space – an entire EMAG production line for steering pinions can be installed on a surface area 15 percent smaller than other standard solutions. The lowered maintenance requirements compared to solutions with portal loaders or robots should also not be underestimated. The vertical design of the machines allows the spindle, slide and parts transport system to be arranged in a very compact form, which also helps to reduce the manufacturing system’s footprint.
The machines in detail
The VTC 100-4 four axis vertical turning machine for shafts clamps raw parts between the central main spindle and the tailstock beneath it. There are two turrets with twelve tool positions available for loading and machining processes with one of the turrets’ tool positions housing a workpiece gripper to transport the shaft in and out of the vertical turning machine. The turrets can be equipped with either turning or driven tools for machining operations. There are endless transport belts on both sides of the machining area.
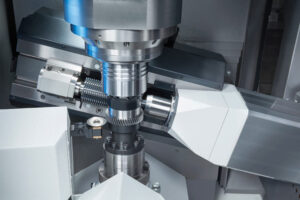
Next a pick-up spindle is used to load the VLC 200 H vertical gear hobbing machine. After the workpiece has been transported into the machining area, KOEPFER’s gear hobbing technology takes charge. The high-performance drive units, which deliver high torques and speeds to the spindle and hob cutter, ensure that toothing up to module 4 can be produced quickly and with high precision. The new VLC 100 IH is responsible for the hardening process. This combines the basic design of the modular machines with the induction hardening technology of eldec, another subsidiary of the EMAG Group. The finish machining of the steering pinions takes place on the VTC 100 GT turning and grinding center. This machine has a disk-type turret with eleven tool positions (the twelfth tool position houses a loading gripper) and a grinding wheel. The benefit of this machine becomes quite clear as the combination of turning operations such as hard or scroll-free turning together with grinding technology ensures a much faster machining process compared to classic final grinding, while still delivering the same quality. The workpiece spindle has a torque of 70 Nm and a drive rating of 17 kW to ensure that the machine has all the necessary power to effectively complete difficult machining processes.
Regardless of how the automobile market develops, EMAG continues to prove that it is perfectly prepared to face future challenges with its products and production solutions. The wide range of technologies available in the EMAG Group allow the company to react flexibly to market developments and also develop unequaled, all-in solutions.