Equipped with a C-axis and Y-axis plus powered tools the NLX 2500 from DMG MORI supports turning operations at Buchholz Hydraulic.
Founded as the handcraft enterprise Buchholz in Kiel in 1884, the Buchholz Hydraulik GmbH of today has concentrated on the solution-orientated development and production of valve controls for mobile hydraulics since 1959. The medium-sized enterprise now has over 300 employees and from its locations in three continents supplies customers from many different branches, including the construction and automotive engineering branches and the maritime industries. In its production, Buchholz Hydraulik trusts in high-quality and high-performance CNC technology in order to meet the high demands placed on
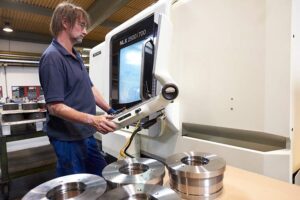
productivity. In October 2014, DMG MORI installed an NLX 2500|700 in the turning division, which, with its C-axis and Y-axis, enables complete machining of the sophisticated workpieces. In addition the new DMG MORI design and the intuitive GUI CELOS® ensure work on the lathe is ergonomic and user friendly.
Fork lifts and excavators are just two examples of the wide field of application of hydraulic solutions. Thanks to its consistent customer orientation Buchholz Hydraulik has established itself as a competent development partner that carries out a project from the concept phase right through to commissioning and optimisation in the vehicle. The core of the work is always the focus on individual product solutions that fulfil the requirements of the customers in respect of functionality and where the question of costs is concerned.
For many years, Buchholz Hydraulik has stood for high product quality and customer-orientated order processing including short delivery times. This high standard is ensured by both well-trained specialists and innovative machine tool technology. Complete machining is an important keyword here, because this kind of production meets the high productivity requirements. In addition to diverse automated systems, Buchholz Hydraulik also upgraded recently in the area of turning where it replaced an old 2-axis lathe with an NLX 2500|700 from DMG MORI.
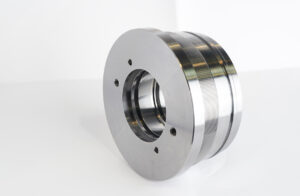
Improved work ergonomics thanks to CELOS® and the new design
Produced for the European market at GILDEMEISTER Italiana, the NLX 2500|700 is available with very customer-specific expansion options so that it can ideally accommodate the specific application required. Buchholz Hydraulik uses a version equipped with a counter-spindle, C-axis and Y-axis as well as powered tools. “This enables us to both turn and mill the workpieces, and what is more, we can do this on the front and the back”, explains Heiko Neßler, the responsible machining technician. This is an enormous gain in productivity compared to the previous solution. “For the simple reason that we no longer need a second machine for milling.”
Another new aspect for Buchholz Hydraulik is the user interface of the NLX 2500|700. Since last year, DMG MORI has been supplying the machine equipped with CELOS® and a 21.5” ERGOline touch display. Operation of the interface is carried out intuitively and DMG MORI achieves a high degree of functionality with this combination of advanced software and hardware. Heiko Neßler programs the job order directly on the underlying MAPPS V control – often parallel to primary machining. One great advantage of CELOS® is its 3D-simulation of the program: “This warns us of potential collisions and also calculates the runtimes of the workpieces.” This option is used for calculations and other work scheduling. The new DMG MORI design rounds off the ergonomic operation of the NLX 2500|700 ab. “The large door provides good access to the work area”, says Heiko Neßler.
Buchholz Hydraulik comes to a very positive conclusion with regard to the NLX 2500|700 and the new CELOS® user interface: it has been possible to integrate machine concept perfectly into everyday production. This verdict is clearly confirmed by the fact that another two NLX 2500|700 machines are to be installed in the coming months.