The performance package hyperMILL MAXX Machining offers three modules for finishing, roughing and drilling that make it possible to achieve impressive boosts in productivity. HEGGEMANN AG, headquartered in Büren, Germany, is a development and manufacturing partner of the aerospace and automotive industry. The company uses hyperMILL to reduce machining times by up to one third on a range of workpieces.
HEGGEMANN AG owner Robert Heggemann manages his company according to the motto ‘360° from Engineering to Production’. He explains what lies behind this approach: “We’re a service provider in the metalworking sector, and we’re in a position to cover the entire process chain from development right through to series production. Our customers are well aware of this. Most of them are in the aerospace and automotive industry and they also value our expertise, reliability, flexibility and quality.”
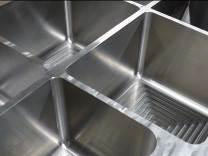
To ensure it is possible to meet the high requirements of a customer industry known for being challenging, HEGGEMANN employs highly qualified staff, both in its engineering and manufacturing operations. Employees define the most efficient manufacturing concept at an early stage during component development and construction. The engineering specialists have broad expertise covering a wide range of materials and production methods, and this is where their skills come into play. What’s more, the company is well equipped with machinery for working with sheet metal and solids. There is a total of 18 milling, turning and hybrid machines available for machining, with most coming from DMG Mori and Hermle. This puts HEGGEMANN in a position to be able to respond to all requirements in terms of complexity and volumes.
Modern software in all areas
HEGGEMANN AG is also state of the art in terms of the software the company uses. The manufacturing management department makes use of a manufacturing execution system (MES) that complies with the latest Industry 4.0 standards. A product data management (PDM) system manages customer data as well as proprietary 2D and 3D CAD data. Once final approval is given by the customer, programmers can access the final data record and generate the required NC programs via CAM.
HEGGEMANN has used the hyperMILL CAM system from OPEN MIND since 2009. It particularly stands out thanks to the innovative hyperMILL MAXX Machining performance package. The ‘5axis tangent plane machining’ strategy in particular has left a lasting impression at HEGGEMANN, as it offers enormous potential for savings, confirms René Reiffer, Head of Production at HEGGEMANN AG.
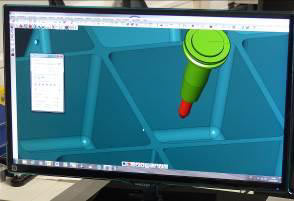
It was Dirk Lehmann, Technical Sales Consultant at OPEN MIND, that originally sparked the interest for the new finishing strategy among Reiffer’s milling team in early 2015 and asked the team to test the 5axis tangent plane machining strategy. The metal removal team got the chance to do just that at the Hermle AG technology centre in Kassel. This is because Hermle, a leading manufacturer of 5axis machining centres, is among HEGGEMANN’s preferred suppliers. “The result immediately won us over,” explains Reiffer. “We now use the 5axis tangent plane machining strategy as often as possible, as we can achieve a significant reduction in machining times.”
A major component of the innovative finishing strategy is the tool it employs – a conical barrel cutter specially developed by OPEN MIND for this purpose. Its geometry has a large radius of 1,000 millimetres or more, allowing enormous line increments during finishing. “We regularly achieve time reductions of 70 to 90 per cent in test workpieces compared with the use of traditional ball mills,” adds Dirk Lehmann.
Finishing time cut from 90 to 15 minutes
Reiffer provides an example of the savings achieved at HEGGEMANN: “We just manufactured a component with deep pockets measuring 155 mm and vertical walls. Until recently, we would have milled it with a 12 mm ball mill, which would have taken about 90 minutes of machining time. Using the new method and a barrel cutter with a lateral radius of 500 mm and a tool radius of 4 mm at the tip, the finishing process only takes 15 minutes. The surface quality was Rz = 3.2 µm in both cases.”
The time saving is primarily due to the barrel cutter’s enormous line increments measuring 4 mm during the final finishing pass. With a ball mill, it would be more than ten times the number of lines at a distance of 0.35 mm.
Reiffer’s team saves additional time when it comes to programming. It takes about 20 minutes to create a finishing programme for a pocket like this with a ball mill. It is possible to program machining jobs for the 5axis tangent plane machining in five minutes.
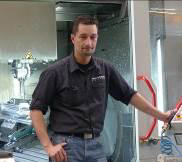
Optimised roughing for 2D, 3D or 5axis operations
The new OPEN MIND performance package also offers other interesting high-performance cutting (HPC) strategies for roughing. For example, the hyperMILL MAXX Machining roughing module allows the user to achieve a maximum stock removal rate by intelligently separating spiral and trochoidal-like tool paths and dynamically adjusting the feed rate to suit the prevailing cutting conditions.
What makes this special is that it can be used for any type of machining operation, be it 2D, 3D or 5axis. HEGGEMANN AG takes full advantage of this possibility. “We mostly use it for 2D components, as we can often machine these components with the entire shank length of the tool,” reports Reiffer, delighted with the time savings. “In cases like this, we are two to three times faster and we also benefit from less tool wear.”
HEGGEMANN also places great value on its excellent cooperation with OPEN MIND. “We receive a top quality service. When we have a question, we get a prompt response by e-mail or by phone. And if it’s really urgent, they’ll send over an application engineer to solve problems directly on site,” says Rene Reiffer.