With the DC170, Walter presents the first representative of a new performance class of carbide drilling tools. Technological progress made visible – with a new design of lands, the DC170 is unique. The copper-coloured finish with unmistakeable channel structure conceals four tangible features of a new performance class for drilling ISO-P and ISO-K materials.
As the new icon of drilling, the DC170 is set to make its appearance on the international stage of metal machining at the IMTEX 2015 in Bangalore. Visibly new, visibly different – a unique design of lands and copper-coloured finish symbolise a new performance class for drills. Walter will be offering the first two models in the dimensions 16xDc and 20xDc. The newly developed DC170 offers more process reliability, stability, running smoothness and efficiency than carbide drills with traditional geometries.
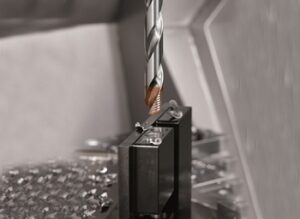
More process reliability
The new drills are internally cooled. Thanks to shallow grooves, the coolant flows unimpeded, while hazardous chip jams are at the same time avoided. Because of the new design of the lands, the liquid washes around the drill continuously, producing a unique cooling effect.
Longer tool life
The solid carbide mass directly behind the cutting edge makes the DC170 incredibly sturdy. Even extreme temperatures are effectively dissipated.
Higher hole quality
An effect of the new type of alignment of the lands is significantly smoother drill running. Because they are continuously guided, vibration is reduced to a minimum, and so the DC170 wins favour across the board.
Less expensive manufacturing
The distinctive cooling channels ensure the optimum operating temperature. Drills straight from the factory are supplied with eight visible channels that can be used as a scale for regrinding. The DC170 drills can be reconditioned up to three times, until only two cooling channels are left remaining. Users who make full use of this now-visible regrinding potential can lower their manufacturing costs.

Helmut Gschrey, Senior Product Manager for Holemaking at Walter AG and one of the pioneers of the new performance class in drilling, explains why Walter has developed the DC170:
The idea
From the start, improving the four most important parameters of the DC170 was our primary concern during the development phase: We wanted to improve tool life – but do so reliably. Secondly, it was very important for us to bring the drill as quickly as possible into a condition of “guidance”, because that’s particularly important during deep-hole drilling where cross holes and inclined exits are involved. The matter of heat exchange was also a development requirement: Given the high temperatures generated during drilling, our intention was for this new generation of drills to be optimally cooled, while they also actively cooled the interface to the material. Finally, we wanted our customers to be able to dispense with the costly business of reworking holes after drilling – and so the new drills had to leave an excellent surface finish.
Feedback from our customer advisors
After the test phases, we can already say that the DC170 enables significant increases in productivity, when gauged against all these four criteria. The fact that our customers always need faster and more favourably priced processes is nothing new. But the challenge is to make that a reality, and continue to do so. With its “Engineering Kompetenz”, Walter is setting a new standard here – and the first customers have confirmed that to us.
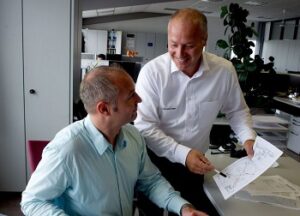
The trend in the requirements for drilling tools
Our customers have to contend with worldwide competition and that drives requirements increasingly higher, especially for high-performance applications. Machining tools supplied to serve this market are therefore also high-tech tools. More productivity than that achieved with the preceding generation of drills is now expected. What needs to be done, anyway, is to also offer these very good tools together with good handling properties and after-sales service, as is provided by regrinding, for example. Tool manufacturers expect to see that they will acquire more responsibility along the entire process chain, in order that customers can concentrate on their core competencies.
Features of DC170:
- Suitable for ISO-P and ISO-K materials in all industries
- Preferable for difficult machining operations such as cross holes and
inclined exits - Upon its launch, available in the lengths of 16xDc and 20xDc
- Proven piloting strategies can continue to be used