Heat resistant super alloys (HRSAs) are an excellent fit for the unrelenting conditions of the oil and gas industry. But the properties that allow it to withstand high temperatures, corrosion and pressure also make them a challenge to machine.
Author: Scott Lewis, Product and Application Specialist, Sandvik Coromant
Just fifteen years ago, the machining of hi-temp alloys was only found in regional pockets in the United States. However, changes in long-standing, yet frequently evolving industries such as aerospace, oil and gas, medical and power has spread the machining of these materials to all corners of the nation. In addition to seeing growth in the use of these materials, we are seeing attempts to create even more heat resistant alloys that increase efficiencies in components such as jet engines and land based turbines.
Unfamiliar territory
As demand for these types of components grows to shops into regions of the country not familiar with their properties, many machining subcontractors are finding themselves in difficult situations after the quoting process. There is a tendency to base machining time assumptions on what that contractor remembers as the worst stainless steel he has ever machined – and then pad that number just to be safe. Shops typically follow machining techniques and best practices for every material they machine. However, if your shop sometimes ignores best practices when machining stainless steel and can still turn a profit, you will find that will not be the case when machining HRSAs.
The bottom line is that HRSAs are extremely tough on tooling. New guidelines, machining techniques and best practices must be followed with these materials or your tools will fail prematurely and you will quickly go through your inventory. The most popular insert used in metal cutting is the 80-degree CNMG insert. But HRSAs wear out CNMG inserts like a NASCAR driver wears out tires. The key to being profitable when machining these materials is to know what you are getting into and applying the right technologies and techniques to get the job done as quickly as possible.
Superior super alloys
HRSAs used in the oil and gas industry are typically metal alloys like Inconel 625 and 718. This nickel-chromium alloy has a high strength-to-weight ratio and superior corrosion-resistance. Its fabricability means that it is easily formed into complex shapes and is readily joined by welding. It is an excellent fit for the power industry as it can readily handle the extreme steam pressures and high temperatures of ultra supercritical plants without any corrosion, such as pitting or crevices.
In addition, HRSAs that come in contact with fluids, such as sea water, require cladding for increased wear and corrosion resistance. Cladding provides a protective coating for components that are usually considered mission critical to safety – like a blow out valve. In other cases, when components are designed to make contact with a corrosive environment, a base metal such an alloy steel is cladded with Inconel 625 or 718. Cladding an inexpensive base material reduces the over all cost of the component. But the welded HRSA is extremely difficult to machine and is much more ductile than an aged and hardened solid component. But keep in mind that although its necessary, cladding is one of the slowest machining processes and almost always causes a bottleneck.
Ultra-supercritical (USC) generation
Traditionally, the aerospace engine business has been the center of the use and development of HRSA’s and that still continues today. But the power industry has taken the same aerospace developments and applied them to land-based gas turbines – which are simply jet engines on land. Steam turbines used in coal-fired and nuclear plants have components that were once machined in stainless steel. However, because of the growing need for more highly efficient coal plants, stainless steel is being replaced with super alloys. Ultra-supercritical (USC) generation is an increase in steam cycle efficiency with undeniable environmental benefits. According to the World Coal Association, modern ultra supercritical generation plants reduce CO2 emissions by up to 40% compared to an average coal-fired plant. HRSAs such as Inconel have opened the door to increased efficiencies because it can withstand the supercritical pressures and superheated steam of this operation.
Shallow and deep wells
In the oil and gas segment of the power industry, deep oil wells are recognized as a high growth area as most of the easy shallow oil wells have already been tapped. Generally speaking, shallow wells produce light, “sweet” crude oil where as deeper wells contain “sour” crude oil. Sour oil has higher concentrations of sulfur and chlorides both of which are extremely corrosive. Therefore many of the extraction activities today involve deep wells that typically produce this corrosive oil. In an effort to resist pitting and sulfide corrosion cracking, more oil and gas down-hole equipment is being made from super alloys since it can withstand this type of corrosion. But the high corrosiveness is only one factor. Deep wells create higher temperatures and pressures, which also creates the need for super alloys. This is not only true of deep sea drilling, but with hydraulic fracking activities as well.
Hydraulic fracturing
Fracking, as it is commonly called, refers to the procedure of creating fractures in rocks and rock formations. Injecting fluid in to these cracks forces them to open which allows more oil and gas to be released so it can be extracted. Fracking, along with horizontal drilling, has opened up new sources of fossil fuels in states like Pennsylvania, New York, and North Dakota. But the characteristics of these wells also require the use of HRSAs. Like the deep oil wells, oil found in these wells is also considered “sour.” Typical stainless steels cannot provide the strength or corrosion resistance to perform well in these conditions. In addition, the extreme pressure created when travelling down to the earth’s shale, which can be seven miles deep, causes extreme pressure on the pipes (up to 25,000 psi or 1,724 bar). Again, HRSAs are able to withstand this extreme pressure because of their high strength, corrosion resistance and ability to resist defying stress cracking and pitting.
Machining techniques to remain profitable
Machining HRSAs is not hopeless or impossible. Once a shop is educated on this type of alloy and understands its uses, it can then plan the most profitable way to machine it. Since we know its tough on tooling, there are some tips and techniques you can apply to make it a smoother process and keep your shop profitable. The key to machining these materials is to make use of the some of the oldest machining techniques and technologies as well as using some new ones.
Optimize the cutting process
Aware of the high fatigue demands of HRSAs, invest in optimizing your process from the start. With a high material cost per part, scrapping components because of a poorly planned process is an expensive lesson that you can avoid. New machine tools and CAM software allow us to do things that were time consuming, if not impossible, just ten years ago. Make the most of these technologies. Again, there is an initial investment, but the pay off can be staggering.
Always use inserts/tools that provide you with a lead angle. While the most popular turning insert in the world is a CNMG 432 held at a -5 degree lead angle, its performance in HRSA is limited due to notch wear. Square inserts held at a 45-degree lead angle, CNMX-SM, as well as round inserts, should always be your first choice in machining HRSAs. Whether it’s for jet engines, power turbines or oil and gas tubular products these components are large, with very few shoulders. Square and round inserts will help redistribute force and give you the best tool life and productivity.
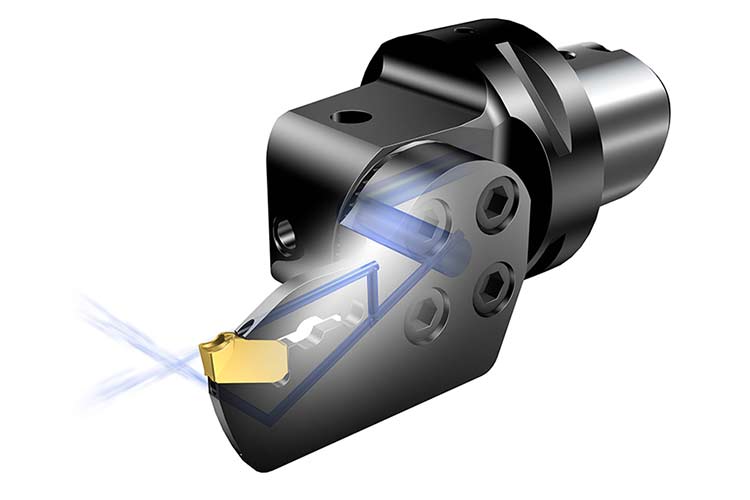
Make use of high-pressure coolant
In addition to the increasing HRSA trend, more shops are using high pressure coolant. High pressure coolant pumps are an easy way to increase tool life and productivity. Although there is an initial investment, if the technology is applied correctly, the return on investment should take less than a year. The great thing about these two trends is that they go hand in hand with of HRSAs driving the increase of pressure in high pressure coolant. Several tooling companies have taken the technology a step further and have created turning geometries designed to specifically to work in high-pressure coolant applications. These geometries are more open with less aggressive chip breakers than normal geometries and use the force of the coolant to break the chip. High pressure, high precision coolant (HPC) directs coolant under and helps lift the chip off the insert thus lowering the temperature at the cutting edge and lessening crater wear to increase tool life and productivity. HPC tools are now offered in many types of platforms. From quick change tools for lathes and modular tools to simple shank tools, customers of all sizes can take advantage of the technology. Even customers running Swiss or sliding head machines for small components can see increased benefits with these tools.
Go modular
Use modular tooling to get away from expensive engineered designs. Aerospace and power turbine components are very similar in nature in terms of shape and complexity. You may feel pressured to purchase an expensive engineered tool from a tooling vendor or you have to find the time to design and build it yourself, drawing manpower away from production machining and putting it into engineering. Today many tooling companies offer an alternative – modular tooling. The idea behind modular tooling is that you can utilize standard products to build a tool assembly allowing you to reduce tool inventory. You can use one tool to fit typical component features and reduce costs by eliminating special tools. The modularity of the tool allows you to replace insert holder components without replacing the entire tool, which is a big cost savings.
Ease the burden with manufacturing economics
Manufacturing economics helps you best utilize your production resources. When machining HRSAs, you can expect that your costs will go up and you will spend more on material and tools. You may spend an increase of up to five to six percent compared to a standard steel application. Since the variable costs are higher when machining these materials, it is imperative to plan a production process that allows you to spread more parts over your fixed costs to increase profitability. Use tooling, new technology and programming techniques to produce more parts in the same amount of time. Although your material and tool costs are sure to go up, if you are using the same number of labor hours, machine hours and overhead to make more parts, your fixed costs become profit for every extra part you produce in that set amount of time.
Invest in education and training
Training and education will help increase the skill level in your shop. On the tooling side, there is great training available. Classes given by tooling producers will allow you to see these techniques and tools in action. In addition, online channels have become a valuable source of information and allow you to see HRSAs being machined. And finally, as energy and super alloys are hot topics these days, there is a wealth of information in trade magazines and on the internet.
Super alloys are in high demand for components used in the power industry for many reasons. HRSAs have a unique ability to withstand extreme heat, pressure and corrosion like no other metal available today. They can tolerate the pressures and temperatures of ultra-supercritical generation to make coal-fired plants super efficient. They can also sustain the heat, pressure and high corrosion found in deep oil wells and in the earth’s shale. But shops new to machining super alloys cannot apply the same rules and practices they have always used with steel and stainless steel and achieve the same results. Machining super alloys is more expensive and can eat up tool inventory if shops aren’t careful. But it is possible to be profitable when machining super alloys. Using the recommended combination of technique, specific tools and training, your shop can be skilled and successful.
Whether it’s for jet engines, power turbines or oil and gas tubular products, large components with very few shoulders need a lead angle to help redistribute force and provide the best tool life and productivity.
High pressure, high precision coolant (HPC) directs coolant under and helps lift the chip off the insert thus lowering the temperature at the cutting edge and lessening crater wear to increase tool life and productivity.