At its Mulhouse plant in Alsace, PSA Peugeot Citroën depends on hyperMILL, a CAM/CAD system from OPEN MIND Technologies AG. The car manufacturer produces aluminium moulds and tools for forging and thermoforming at the plant. Since introducing hyperMILL, PSA has benefited from the numerous options for automation offered by NC programming.
In the past, PSA employees had to write their own macros if they wanted to make it easier to program recurring geometric shapes. The macros were time-consuming to maintain, and constantly had to be adapted to new software versions. In the search for new CAM software, hyperMILL stood out as the obvious choice because it offers numerous options for automated programming; intelligent macros are just one example. Today, the software is being used in all areas.
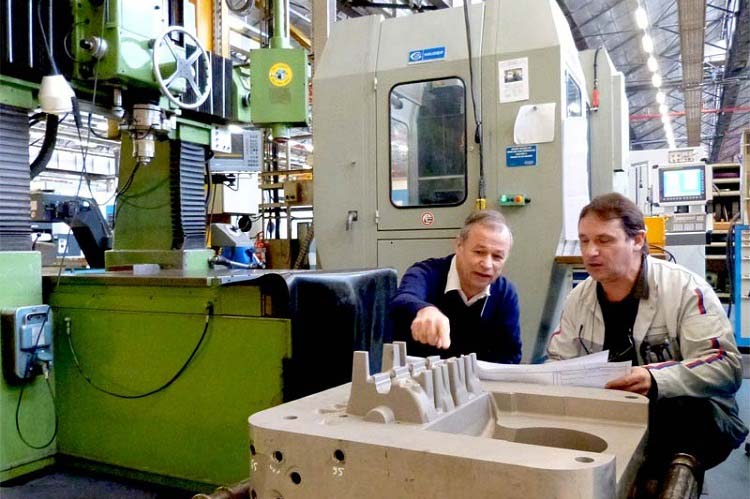
“hyperMILL® is a forward-looking solution offering innovative technologies for 2D, 3D, HSC, mill/turn and 5x machining. We were impressed by its intuitive user interface, its simple and transparent management of complex processes and its straightforward way of including user-defined macro instructions and maintaining them in later versions,” reports Laurent Sifferlen, who is responsible for tool and CAD/CAM quality in the PSA workgroup.
Serge Locher, a programmer at PSA, explains: “We were able to automate the transfer of CAD models from CATIA, and discovered in the process that we were able to eliminate all of the sources of errors that can arise during automation, for example during drilling. We could reuse our macro instructions for drilling or machining work and use them to create new instructions directly in hyperMILL.”
Roughing with hyperMAXX
The PSA plant in Mulhouse employs hyperMAXX, a high-performance cutting module. Fully integrated into hyperMILL®, this roughing module ensures optimal milling paths and maximum material removal. It translates into time savings of roughly 30 per cent for PSA, while also drastically reducing wear and tear on tools.