At the Diemould exhibition taking place at Bangalore International Exhibition Centre, Bangalore, India, from 6-9 April, Renishaw (hall 2A stand B38) will highlight a range of process control solutions that help tackle the increasing drive to lean manufacturing, from new technologies for pre-process machine calibration, to on-line and off-line post-process measurement. There will also be a significant focus on the company’s additive manufacturing (3D printing) systems with the new PlusPac™ upgrade for its AM250 additive manufacturing machine.
The company will have active demonstrations of its Equator gauging system along with various machine tool software’s catering to Diemould industry.
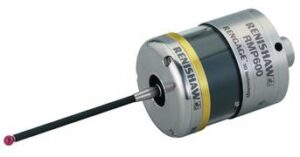
Renishaw is the UK’s only manufacturer of a machine that ‘prints’ metal parts and visitors to the Renishaw stand will be able to see applications that demonstrate the capabilities of the company’s additive manufacturing technology and Strain gauge high-accuracy machine tool touch probes – Unparalleled accuracy and repeatability make this technology the best choice for complex multi-axis work and machine calibration .
RENGAGE™ technology
RENGAGE™ technology delivers true three dimensional (3D) measurement performance and submicron repeatability. So for exceptional performance, reliability and durability, why choose anything less? Conventional probes continue to fulfil a valuable role, which is why Renishaw maintains its position as market leader in the design, manufacture and support of these products.
However, for numerous applications, the significant performance benefits offered by RENGAGE technology provide users with a competitive advantage, for both now and the future.
RENGAGE technology is available with radio transmission in the RMP600; with optical transmission in the ultra-compact OMP400 and compact OMP600; and in the miniature MP250, offering an unmatched combination of size and accuracy.
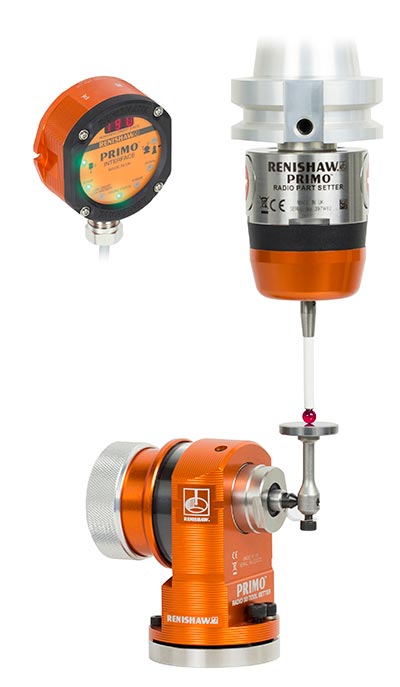
The Primo™ system – opening up the world of precision manufacturing
At Diemould Renishaw is highlighting the Primo system: an entry‑level machine tool probing system that opens up the world of precision manufacturing to all types of manufacturing operation.
A genuine breakthrough business model, the Primo system makes it easy for manufacturers to take their first steps towards higher-value manufacturing by automating their operations and achieving repeatable processes.
Renishaw fixtures: the new single source for metrology fixturing
Following the acquisition of R&R Sales LLC in 2012, Renishaw has developed an extensive new range of modular fixturing designed specifically for co-ordinate measuring machines (CMMs), vision systems and its Equator™ gauging system. Visitors to Diemould 2016 will see that the new range offers a wide choice of base plates and components available in M4, M6 and M8 thread sizes, and can be utilised for measurement applications across multiple industries, such as aerospace, automotive and medical.
Automated gauging and process monitoring software for the Equator™ gauge
Renishaw Equator™, a lightweight, fast and highly repeatable gauge, will be demonstrated in an automated cell. Equator’s innovative flexible gauging technology is based on the comparison of production parts to a reference master part, which can greatly increase throughput and reduce scrap rates at a fraction of the cost of an equivalent custom gauging system. Equator can switch between parts in seconds, perfect for flexible manufacturing processes or accepting parts from multiple machines.
A new process monitoring window has also been added to the shop-floor user interface for the Equator gauging system. This instantly displays measurement results of inspected features to the operator on a bar-graph display. It also shows the history of measurement on each feature so that process trends can be seen. The system’s re-mastering process can now be managed based on temperature limits, number of parts or time since last master.

Enhancements in metal 3D printing
Visitors to Diemould will also see a new range of additive manufacturing technologies. Renishaw’s laser melting systems utilise a pioneering, additive manufacturing process capable of producing fully dense metal parts direct from 3D CAD, using a high-powered fibre laser. Parts are built from a range of fine metal powders that are fully melted in a tightly controlled atmosphere, in layer thicknesses ranging from 20 to 100 microns.
The AM250, Renishaw’s first additive manufacturing machine is now available with PlusPac – an add-on kit which transforms the machine to meet the demand for cleaner process environments, improved surface finish and precision. PlusPac includes new Optical Control Software (OCS), a gas knife lens window protection system, and a high capacity filtration system. These updates give the user tighter control over the build process, enabling users to create even better components.