With significantly longer tool life and improved edge utilisation in field tests, Kennametal’s newly launched Beyond DriveTM portfolio of cutting inserts are being called the new gold standard for turning. Adding a new titanium oxycarbonitride outer coating (TiOCN) not only increases wear- and abrasion resistance for lower temperatures and longer tool life, its bronze color is an effective wear indicator as opposed to black surfaced inserts. Where inserts had been thrown away early in favour of safety because of poor wear identification, operators are now reporting notably longer service life per edge, even in aggressive environments. Depending on the application, field tests are showing up to 30% more parts per edge.
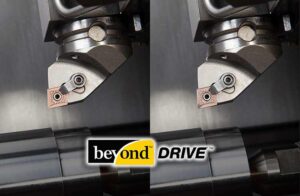
Beyond Drive is an entire portfolio of new grades and geometries that emphasise ease of selection and use across work materials and turning conditions. Specific customer demands addressed by Beyond Drive include reduction of notch wear in demanding applications and reduction of crater wear in difficult materials, all while improving wear identification.
Beyond Drive is specifically designed for leveraging improved performance and longer life in many critical turning tasks across steels, stainless steels, cast irons, and high temperature alloys. By cutting costs, avoiding waste, and producing many more high erquality parts per cutting edge, manufacturers in transportation, energy, general engineering, and more are taking a significant leap forward in productivity and increased capacity.
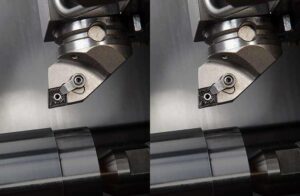
“For example, the Beyond Drive MR (medium roughing) insert has a high positive rake angle that works with the smoothly curved cutting edge to reduce cutting forces and extend tool life. In terms of chip flow, it ́s like nothing ever seen before,” says Lothar Unglaub, Kennametal turning expert.
Indexable double sided inserts are subject to high cutting forces, and are commonly seen as less stable. MR ́s rake profile without the points of load concentration results in an extremely stable insert body, despite the high positive rake. Even with high depth of cut applications, turning processes are safer and more stable, ensuring lower load on the machine tool and workpiece. Additionally, MR inserts also feature formed-in coolant channels that deliver flood coolant efficiently to the cutting edge. Improved heat control translates into smoother cutting and extended tool life.
Total System Solutions
Adding the benefit of increased stability to Beyond Drive ́s design and performance advantages Kennametal ́s KM4XTM spindle connection. Sizing the right spindle connection with the machine tool helps optimize the productivity of the entire system. The combination of the KM4X system ́s high clamping force and interference level leads to a robust connection and extremely high stiffness and bending capacity for greatly improved performance. KM4X overcomes the limitation on bending capacity present in other connections, allowing maximum available spindle power and torque to be utilised in critical operations like turning of high strength materials.
In short, the KM4X connection is capable of performing right up to the machine tool ́s full potential, which drives the most out of the cutting edge, Combined with the latest Beyond Drive portfolio, turning can be far more productive and cost effective.
Another advantage is running dry, where Beyond Drive performs very well. Coolants can cost a lot of money and add processing and disposal concerns. Even in very aggressive turning environments involving external scale or heavy, interrupted cuts, Beyond Drive is showing increased performance.
For example, in one test for a plant producing castiron transmission components, with no change in feed, spindle speed, or depth of cut, Beyond Drive completed 325 pieces per cutting edge compared to 200 pieces for the plant’s current inserts. Not only was this a phenomenal increase in parts per edge, projected machine hours freed per year totaled 125 while the number of inserts required per year dropped from 813 to 500.
A stronger supply chain that gets more parts to market reliably is the foundation of a healthy and growing manufacturing industry. Beyond Drive is a truly exciting development that promises more higher quality parts per shift, more efficient machine utilization, and longer tool life.