Makino plans to share its latest solutions for plastics processing March 23-27 at NPE2015 in Orlando, Fla. Booth S8125 is slated to showcase solutions for a variety of industries, including medical, automotive and aerospace molds.
“The global automotive, medical and packaging markets are growing rapidly, and this show is a great place for manufacturers to learn how to meet increasingly stringent requirements for quality and lead-times, such as lighter-weight vehicles in the automotive industry,” said Mark Rentschler, director of marketing at Makino. “Visitors to Makino’s booth will meet with our applications engineers to discover new machining and wire EDM process and technology solutions to meet such requirements.”
Sustained Dynamic Accuracy
Makino plans to include the D300 5-axis vertical machining center. The D300 is designed to deliver superior sustained dynamic accuracy in full five-face machining applications. Equipped with core-cooled ballscrews and temperature-controlled direct-drive motors and spindle, the D300 provides thermally stable machining conditions for the highest degree of precision and finishing quality. The design of the direct-drive rotary axes gives manufacturers the speed and positioning repeatability to be productive in a wide variety of complex, 3-D workpieces.
The machine comes standardly equipped with a 15,000-rpm HSK-A63 spindle with 120Nm (42Nm continuous) of torque for flexible, high-speed machining of various workpiece materials, including steel, aluminum and titanium. Optional spindle configurations consist of a 20,000-rpm HSK-A63 spindle and 30,000-rpm HSK-F63 spindle.
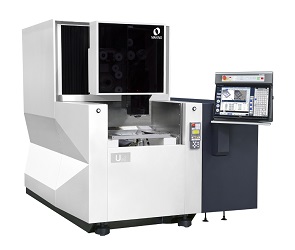
A Versatile Solution
Also slated to be showcased is the U3 Wire EDM. Designed for ease of operation, versatility and low operating cost, the U3 is the next-generation solution for improved profitability in wire EDM processes. With the addition of Makino’s new HyperCut technology and Hyper-i control, even novice operators can program and produce leading-edge part finishes in the most complex feature geometries with the U3. A user-friendly interface similar to that found on tablets and smartphones makes operation very intuitive. This is a significant competitive advantage for shops experiencing difficulty replacing skilled EDM operators.
The U3 offers X-, Y- and Z-axis travels of 370mm by 270mm by 220mm, respectively. The U3 can accommodate a maximum workpiece size of 770mm by 590mm by 220mm, with a payload of 1,322 lbs. Other features of the U3 are reduced wire-consumption rates, dual digitally controlled flush pumps and a choice of two wire-guide configurations—conventional round or Split V guide system—to accommodate any material types and flushing conditions from 0.004″ to 0.012″Ø wire (0.1~0.3mmØ). An extensive cutting condition library provides optimized conditions for standard hard brass wires, high-speed coated wires and high-taper soft wires. The depth and versatility of the entire cutting condition library ensure that all applications can be machined at optimum productive levels.