GF Machining Solutions’ latest-generation MIKRON HPM 600U and HPM 800U five-axis, simultaneous Milling centers deliver increased speed, powerful machine control, spindle protection and state-of-the-art chip management for greater flexibility and more success. Renowned as a compact, fully automated, five-axis, high output, machining solution, the new HPM 600U/800U machines promise to take machining operations to the next level.
Designed for tool and mold making and for the production of high-quality components, the HPM 600U and HPM 800U can be configured for manual loading or with fully automatic pallet magazines with corresponding handling of large tool volumes. The series features powerful drives on the X, Y and Z axes and direct drives on the rotary and swiveling axes. Together, these characteristics form the foundation for highest dynamic and economical machining and pave the way to optimum automatic loading of workpieces (pallet changer) and tool magazines from 30 up to 210 tools. Plus, the view of the working space is always clear, even on the fully automated version.
Although they are sturdy and highly compact, the machines have a large working space. The HPM 800U, for example, has maximum X-Y traverse paths of 800 x 800 mm. The machine’s Z axis offers a clear width of 700 mm from the table surface to the spindle nose. This large working space means cylindrical workpieces can be machined with a diameter of up to 800 mm. The cleverly selected circular swiveling table dimensions make it possible to machine workpieces up to 600 mm in height with 100 mm long tools on all sides.
Siemens control opens door to new applications
Siemens’ premium-class SINUMERIK 840D sl control (CNC) is now available for the HPM 600U/800U series. This drive-based, modular CNC opens the door to new and challenging applications for mold and die, including production of molds for plastic parts in automotive, and housings for printers, televisions and other electronics. In aerospace production, the SINUMERIK 840D sl easily allows five-axis simultaneous Milling of flow parts like impellers and blisks for the aerospace and energy industries.
Continuity from the CAD program all the way through the workpiece is a hallmark of the SINUMERIK 840D sl. Its intelligent motion control allows fast, precise production of even highly complex parts. Alterations are simplified by the separation of geometry and technology with remote tool center point (RTCP) and 3D tool offset.
New motor spindle’s proven advantages
Already proven successful on existing MIKRON machines with the Siemens SINUMERIK 840D sl control, Step-Tec’s 20,000 min-1 HPC 190 motor spindle is now standard to HPM 600U/800U machines with the Heidenhain iTNC 530 CNC.
The new 20,000 rpm motor spindle delivers a very large number of proven advantages. Customers can benefit from lower tool wear due to higher stability provided by 30 percent greater tool holder clamping force and a 10 percent larger shaft- and bearing diameter. Moreover, compared to its predecessor, the new motor spindle consumes 30 percent less compressed air and emits 20 percent less heat. In comparison with the shaft of an inline spindle, the motor spindle’s significantly shorter rotating shaft generates less vibration at top speed and 40 percent more precise tool run out; that ensures longer tool life and a much better workpiece surface. The new motor spindle also boasts 40 percent higher torque, eight coolant nozzles situated 180 degrees around the tool, and two integrated LED lamps for best illumination of the working area.
Available for the HPM 600U/800U is the Step-Tec 28,000 min-1 HSK-163 motor spindle with patented shaft-cooling CoolCore technology. CoolCore water cooling of the rotor shaft ensures that temperature and expansion of the rotor shaft are stable.
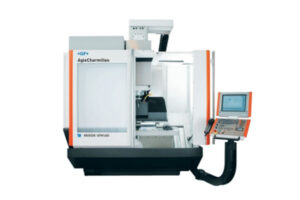
Machine and Spindle Protection (MSP)
GF Machining Solutions’ available MSP protects the machine and spindle during the setup process. Crashes occur primarily during the first use of a new CNC program. In safe mode, the feed rates are reduced to a speed that allows common cutting operations, guaranteeing that the spindle and machine are protected against crash-related damage. When production conditions mandate fast feed rates, the mode is standard and the machine can move the axes at full speed. A three-year warranty on the spindle against crash is standard with MSP and can be extended by up to five years to a total of eight years.
State-of-the-art chip management
Because high-performance Milling generates large quantities of chips that need to be reliably conveyed out of the working space, GF Machining Solutions is constantly innovating to improve chip management. The HPM 600U/800U machining centers feature the newest chip management system, allowing customers to choose the solution that best suits their needs, depending on the chip material and shape.
Chip management system options include:
- lift-up scraper and lift-up slat band chip conveyors,
- pump back station,
- chip trolley,
- 450-liter basket filter system,
- 950-liter band filter system,
- 950-liter and 1,850-liter endless belt filter systems,
- 15 – 40 bar and 18 – 80 bar through-spindle coolant (TSC),
- wash-down system,
- oil skimmer,
- coolant thermal control.
Toward a balanced, highly-customized system
Performance and flexibility are essential for success, and the HPM 600U/800U’s new features represent a balanced, highly customized system that puts customers in the driver’s seat to control operating costs and ramp up quality. Greater versatility can be achieved by using various sizes of tool magazines and by choosing pallet handling: two, seven, and nine or 12 pallets. High Dynamics (HD) versions of the HPM 600U and HPM 800U are also available, with axis accelerations of 1.7 g and speeds of up to 60 m/min.