Until today it has been difficult to directly clamp on a quick-change pallet system large workpieces due to thermal dynamics, inherent stress or other difficulties in accurately mounting clamping pins for quick-change pallets. SCHUNK, the competence leader for clamping technology and gripping systems provides the right solution. The SCHUNK VERO-S SPD clamping pins compensate in a range of +/- 1 mm and pave the way to efficient direct clamping.
In order to use this effect, the SCHUNK VERO-S quick-change pallet modules are briefly open for finish machining, and therefore a tension-free state is achieved. When the modules are relocked, the flexibility of the VERO-S SPD clamping pins avoids that the workpiece will deform again, and high precision results are achieved. The flexible clamping pins are available in two versions: the SCHUNK VERO-S SPD-B, which allows the compensation of +/- 1mm in one direction, and the SCHUNK VERO-S SPD-C, which compensates +/- 1 mm in diameter. The flexible clamping pins can be used with every SCHUNK VERO-S NSE plus module. As all the SCHUNK VERO-S components, the SCHUNK SPD clamping pins are also manufactured from stainless steel. They are connected with the workpiece with standard (M10) screws. The holding force amounts to 35 kN.
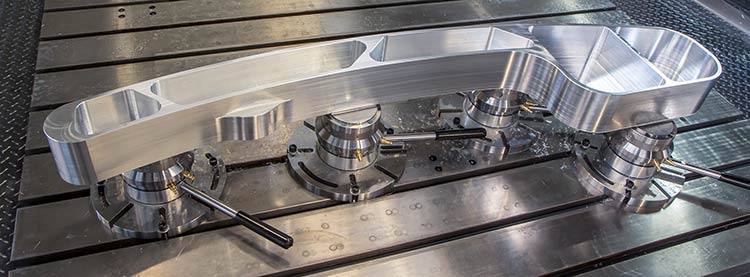
Direct clamping has numerous advantages
For direct workpiece clamping with the SCHUNK VERO-S, users do not need conventional clamping equipment such as clamping claws or lathe chucks with several chuck jaws. Instead, mold plates, freeform plates and other workpieces are initially surface milled at the base plate to the same level with defined tapped holes and are then equipped with clamping pins of the quick-change pallet system. The parts can be exchanged in the machine with quick-change pallet modules within a few seconds, and are immediately precisely clamped. In comparison to the conventional clamping solutions, there are no interfering contours around the edges from chuck jaws or clamps in case of a direct clamping solution, so 5-sided machining with maximum accessibility is ensured. Plus unproductive downtimes just like time-consuming set-up, retooling, aligning or determining the zero point can be eliminated from the machine consistently. Direct clamping is similarly effective, if workpieces are repeatedly modified or have to be machined under deadline. Due to the existing tapped holes the parts can be exchanged on the machine very precisely and within a very short time.